增材制造 (AM) 开创了数字制造的新时代,工程实践、计算机辅助设计平台和零件采购渠道正在逐渐发生巨大变化。AM 增材制造技术能够生产塑料、金属和陶瓷组件,用于原型设计和最终用途。从历史的角度讨论了七种3D打印技术制造致密、结构先进的陶瓷部件。陶瓷增材制造的工业应用比金属和塑料材料大概晚十多年,这其中陶瓷增材制造的许多挑战可以追溯到加工结构陶瓷材料的内在困难,包括加工温度高、对缺陷敏感的机械性能和加工特性差。为使陶瓷增材制造领域成熟,未来的研发应着眼于扩大材料选择,改进3D打印和后处理控制,以及多材料和混合加工等独特能力。图片
2017年-2021年, 是基于光固化的陶瓷3D打印在航空、医疗领域得到应用发展的五年。同样是在这五年中,粘结剂喷射3D打印技术在模具、铸造型芯制造中的应用得到加强,陶瓷3D打印企业发力于生产级的陶瓷3D打印系统与材料的研发,同时更低成本与更高精度的3D打印技术进入市场。随着陶瓷增材制造技术与材料技术的继续发展,基于光固化、粘结剂喷射、材料挤出3D打印技术的应用将得到不同程度的加强,应用领域预计将扩展至汽车、牙科、能源、电子等更多领域。
3D科学谷《3D打印与陶瓷白皮书》
一、介绍
1.1.前言
在这篇综述中,详细介绍了大块致密结构陶瓷的增材制造 (AM) 的历史、最新进展和未来方向。由于其高硬度、耐磨性和耐腐蚀性,先进陶瓷在结构应用中很有吸引力。
为了实现这些特性,结构陶瓷需要大于 95% 的相对密度,许多应用(例如装甲陶瓷)需要高于 98% 的相对密度。高硬度和耐磨性能使加工过程复杂化;陶瓷增材制造研究是由对制造复杂组件的成本效益高的方法的需求推动的。本文通过对陶瓷增材制造发展的历史分析,为陶瓷增材制造的发展趋势提供了一定的逻辑判断基础。
1.2.先进陶瓷及其应用
高级陶瓷具有出色的耐磨性、耐腐蚀性和耐高温性。这些材料可以是生物相容的、电激活的和光学活性的。应用几乎涵盖所有行业,重点是航空航天、汽车、国防、医疗和能源领域。发动机部件、车身和车辆装甲以及承重医疗植入物都依赖于致密的结构先进陶瓷。
3D科学谷《3D打印与陶瓷白皮书》
3D科学谷《3D打印与陶瓷白皮书》
陶瓷成型是一种成熟的技术,具有商业制造规模的多种方法,例如压制、挤出、泥浆浇铸、流延浇铸、凝胶浇铸和注塑成型。然而,这些传统的成型技术通常只允许二维设计自由,无法创建内部或多尺度特征,并且需要复杂且昂贵的模具。
此外,由于传统粉末混合和加工的随机性,化学异质结构的工程设计受到限制。没有二次分层步骤的流延带仅允许控制片材厚度。压制和挤压生产简单几何形状的零件,如圆盘、棒和管 。滑动浇铸、凝胶浇铸和注塑成型提供了最大的几何自由度,但不能实现材料的异质性。除了分层流延试样,其中层可能是不同的材料,这些技术都生产化学均质的部件。此外,由于高级陶瓷具有出色的耐磨性,因此机加工既费时又费钱。事实上,致密高级陶瓷零件的加工占生产成本的 80% 以上。
1.3.增材制造
相反,增材制造 (AM) 能够生产具有复杂、多尺度几何形状的零件,包括内部结构。此外,多材料 AM 允许通过离散层和成分梯度来定制材料异质性 。ISO/ASTM 标准 52900:2015(E) 将 AM 工艺的基本原理定义为“通过连续添加材料形成三维零件”。增材工艺之间分类为七个 AM 技术系列:光聚合、粉末床熔化、粘结剂喷射、材料喷射、片材层压、材料挤出和定向能量沉积 。
这些工艺在表 1 中进行了描述,其信息包括材料选择、特性、优缺点以及机械性能和微观结构。AM 是通过单步过程(通常称为“直接”)或多步过程(通常称为“间接”)实现的。图 1 说明了同时产生具有最终性能的所需形状的直接工艺与需要两个或更多步骤才能产生具有最终性能的所需几何形状的间接工艺之间的区别。金属、陶瓷和聚合物材料都适用于这些 AM 工艺,从而能够生产原型和最终使用组件。
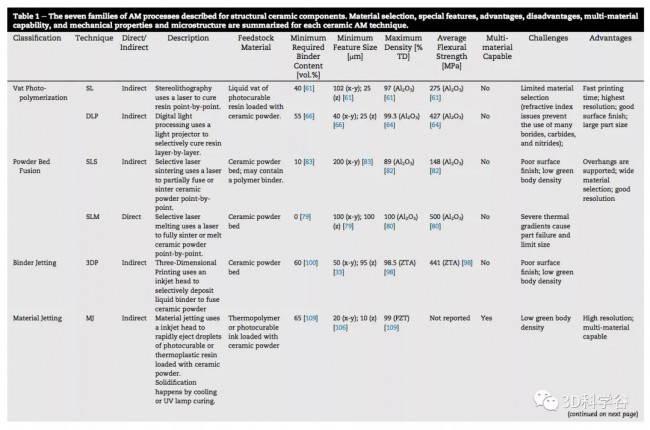 表 1. 针对结构陶瓷部件描述的七类增材制造工艺。总结了每种陶瓷 AM 技术的材料选择、特性、优点、缺点、多材料能力以及机械性能和微观结构。
图 1. 直接增材制造工艺同时产生具有最终特性的所需形状,而间接工艺需要两个或多个步骤才能产生所需的几何形状具有最终属性。对于陶瓷材料,在使用间接工艺形成生坯后,必须进行热解和烧结才能获得最终性能。
增材制造最适合复杂几何形状的小批量生产,因为时间和成本对复杂性的依赖程度较弱,增材制造能够制造通过减材制造或成型工艺无法实现的复杂几何形状。
重要的是要注意,AM 生产的零件的机械性能在很大程度上是各向异性的 。事实上,术语“3D 打印”用词不当,因为打印是在构建方向上逐层重复的一维或二维过程。出于这个原因,机械性能将根据相对于构建方向的测试方向而有所不同。
(责任编辑:admin) |