来源:复合材料学报. 2024年第9期
作者:李家雨, 付宇彤, 李元庆, 等. 增材制造仿生结构的力学性能优化及其功能设计研究进展[J]. 复合材料学报, 2024, 41(9): 4435-4456. doi:10.13801/j.cnki.fhclxb.20240423.004
仿生结构能够在一定程度上克服传统结构和材料的缺陷,从而实现高性能和功能的多样化。增材制造(3D打印)技术可以实现复杂结构的成型,从而可以制备出具有优越力学性能和更多样化功能的仿生结构。随着增材制造技术的不断发展,增材制造技术与仿生结构设计的结合越来越受到人们的关注。同时,增材制造仿生结构具有良好的力学性能和功能,在航空航天、轨道交通、机械工业、生物医学工程等领域受到关注。本文总结了近年来3D打印仿生结构的研究进展,主要集中在力学性能优化和功能方面。优化的力学性能主要包括吸能、高强度、高刚度等,而功能则与传感、驾驶、医学等有关。最后,本文对增材制造仿生结构的优势、现有研究局限性和未来发展进行了总结和展望。
仿生结构受自然界动植物巧妙结构的启发,通常会表现出卓越的力学性能;同时,这类结构也受动植物维系生命功能天然设计的启发,能够表现出多种功能特性[1]。得益于仿生结构突出的力学性能和强大的功能特性,其在航空航天、新能源、轨道交通甚至医学等领域都具有广泛的应用背景。
为实现不同性质、不同功能,可对不同生物结构进行仿生设计。部分生物结构具有高强度、高韧性等优异力学性能[1],事实证明这些天然生物材料拥有优异的力学性能来源于其层次性结构[2],例如骨骼表现出高强度和韧性就是由于其7个层次结构中的多种机制[3-6],而蜘蛛丝的高抗拉强度和大延展性则归因于其复杂的层次结构[7-8],这使其在对力学性能敏感领域的运用具有天然的优势,力学性能优化的仿生结构应运而生。这些仿生结构通过借鉴天然动植物,将管状、夹心、蜂窝结构引入设计中,实现吸能、强度、刚度上的改良,同时因这些天然生物材料多层级的特点,利用增材制造技术制备结构复杂精巧,接近于天然结构的仿生构型是相较于传统制备方法更合适的一种选择。此外,为了让材料和结构拥有多功能性、高性能、智能响应等特性,可通过仿生设计来改善材料组分、细化内部结构。目前航天航空、机械工程及生物医学领域较重要的功能仿生结构主要和传感、驱动、愈合等相关。传感仿生结构往往具有高灵敏度、选择性、稳定性及可靠性等特征,它们可以实现复杂自然和生理环境的监测[9]。驱动仿生结构主要通过模仿不同生物的运动和结构来实现驱动功能,而不同的仿生模式会使它们拥有不同的输出机制。这些具有驱动功能的仿生结构往往因其高输出力、高速度、高分辨率等特点具有广泛的应用[10]。具有医学功能的仿生结构则是从天然生物的结构、功能和行为中寻找灵感,并将生物学原理和材料科学和工程相结合,从而促进生物材料、药物运输、组织工程、医疗设备和仿生假肢等各个领域的创新[11]。本文将对图1[12-25]所示的力学和功能特性进行总结,并介绍目前增材制造(3D打印)仿生结构及其功能的研究发展。当今,增材制造因其在制造复杂结构、设计自由度、减少浪费和节约成本等方面的突出优势,已成为一大研究热门[26]。加之其高效率、高灵活性的特点,目前在轨道交通、航空航天、生物医学等众多领域也已具有广泛应用[27-29]。此外增材制造在仿生设计中的应用也早已变得十分深入,增材制造对于很多复杂的生物结构的成型是一个很好的解决方案,其灵活的成型方式不仅能够打印出很多复杂的生物结构,而且还能够根据不同材料的组合打印出不同性能的仿生结构[26],但在常见的增材制造方法当中,例如材料挤压[30]、材料喷射[31]这两种机制的增材制造方法在打印上可能会存在表面质量差、印刷速度慢及尺寸受限等问题,这也是增材制造当中必须解决的难题[32]。
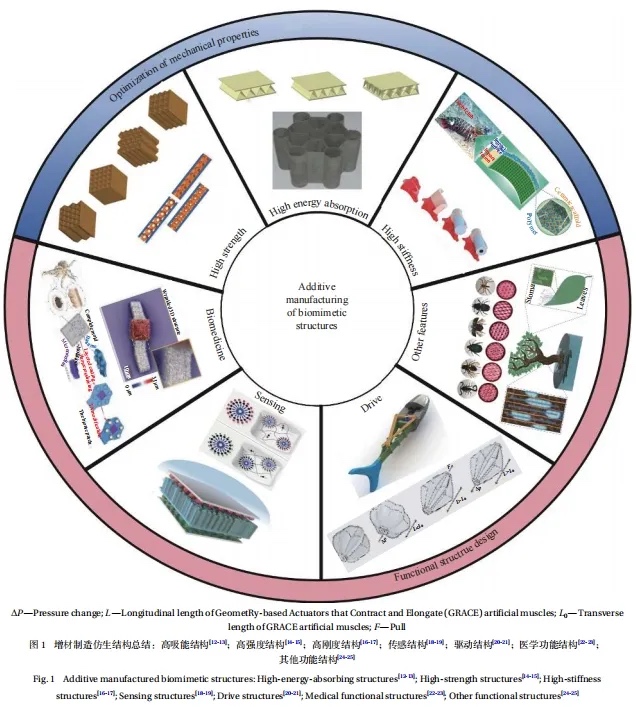
图1
仿生学是一门古老而又年轻的学科,但是受传统加工方式的制约,很多仿生结构难以利用传统技术制造出来。增材制造技术作为近年来快速发展的一项先进制造技术,其逐层累加材料实现成型的过程与自然界的生长方式十分契合,因此能够制造结构复杂的零部件,从而促进仿生学的发展[33]。但是,当前仿生结构的性能可能受到增材制造中成型缺陷的影响,因此想要将增材制造技术和仿生结构设计结合得更好,还需要更多的努力。总而言之,随着增材制造技术的发展,其与仿生结构设计的结合在未来会越来越成熟,增材制造仿生结构将会在更多领域发挥至关重要的作用。
本文将重点介绍增材制造仿生结构在性能优化和功能上的实现情况。本文第一节主要介绍仿生结构在力学性能上的优化,第二节将从形态仿生、结构仿生、功能仿生等不同类型的仿生结构总结国内外学者的研究进展。
1 3D打印仿生结构力学性能优化
自然界中的多种动物、植物在长期进化过程中形成了独特的轻质、高强结构,以此来抵抗外界的复杂冲击荷载来保护自身的完整,满足生存的需要。生物轻质高强结构的优越性启发了科研和工程人员采用结构仿生学的方法来优化结构的力学性能。例如,通过借鉴自然界中竹子、瓢虫、肌腱等生物结构,发展具有轻质高强特点的仿生结构。随着增材制造技术的蓬勃发展,复杂的仿生结构得以实现。3D打印仿生结构可以在吸能、强度、刚度等力学性能上对传统结构优化。国内外学者通过仿生学和增材制造技术设计制备了仿生吸能结构、高强度结构、高刚度结构。这些结构在航空航天、汽车和体育器材等对强度、刚度有严苛需求的行业具有很好的应用前景。本文总结的仿生结构在力学性能上的优化情况如表1所示[12-17, 34-48]。
表1
1.1 吸能
仿生吸能结构借鉴了自然界中生物体的特性,通过模仿它们的结构和受力机制,实现吸收和分散能量的功能。国内外学者受自然界中的管状结构、泡沫结构、夹心结构等的启发设计了具有强大吸能特性的复杂结构,利用增材制造技术实现制备,并在航空航天、汽车和体育器材等领域被广泛应用。
1.1.1 管状结构
薄壁管状结构具有大变形能力和稳定的变形模式,同时由于它多孔的内部结构使其具有强大的吸能能力。无论在宏观和微观上,生物结构中都存在着管状结构。例如宏观的竹子杆部常为由节间和节连接而成的圆筒形,甲虫前翅和肌腱的内部微观结构都存在着杆状的结构,这些动植物天然的管状结构使他们具有强大的抗冲击能力,从而具有强大的吸能特性。很多学者受到这些管状结构的启发,利用增材制造技术实现仿生管状结构的快速制造,从而使仿生结构的吸能特性得到了优化。
Zou等[12]分析了竹子维管束的梯度分布及维管束与薄壁细胞的有机结合(又称基质组织)是维持竹子优异力学性能的主要原因,并受竹子内部结构启发,设计了一种由1个仿生节点和3个仿生内管组成的薄壁吸能抗冲击结构(图2(a))。在冲击实验中,此薄壁结构的单位质量吸收能量(Specific absorption,SEA)为35.03 J/g。Hu等[13]通过将中央圆管连接到其他6个六边形排列的圆管来模仿竹维管束微结构的特征,提出了一种嵌套蜂窝管结构(Bionic honeycomb tubular nested structure,BHTNS)(图2(b))。在轴向冲击实验中,BHTNS展示出良好的能量吸收性能,其最大比吸收能量是51.7 J/g,高于传统金属蜂窝结构(35 J/g)和新型自相似规律性分叉蜂窝(最大42 J/g)。
图2
瓢虫鞘翅的内部微观结构中,存在许多形状的小型独立薄壁结构,包括三角形、矩形、六边形和圆形,并且在这些独立薄壁结构中心还存在一个空心圆柱管,这种双管薄壁结构就起到保护其翅膀和身体免受伤害的作用,因此Xiang等[34]模仿瓢虫前翅特征通过引入不同多边形截面组成的各种圆形管,设计出一种新型仿生双管薄壁结构(Bionic bi-tubular thin-walledstructure,BBTS)(图2(c))。在轴向动态冲击载荷作用下,当内壁厚度在1.6 mm至2.0 mm时,该结构表现出最佳的碰撞性能。此外,当内壁厚度为2.0 mm时,圆形和八角形BBTS显示出更好的吸能特点,优化的BBTS结构在能量吸收能力方面比原始的仿生结构提高了10%。
肌腱的横截面上存在7个层次结构,尺度从纳米、微米到毫米不等,胶原蛋白分子在纵向和横向上聚集形成原纤维,这些原纤维紧密地排列在不同层次结构中控制着肌腱的强度和韧性,本质上这些都是一个单向结构,但不同阶数结构的组合使肌腱具有强大的力学性能,因此Tsang和Raza[35]根据这一特点设计了可以利用增材制造技术生产制备的仿肌腱管状分层管(图2(d)),发现当层次结构嵌套了该管状结构后,二阶分层管和三阶分层管相较于一阶管的峰值总能量分别减少了75%和89%。因此引入该层次结构显著提升了层次结构的能量吸收能力。这些仿生薄壁管状结构相较于传统管状结构在吸能特性上得到了显著的提升。不仅仅对于管状结构,泡沫结构也是一种理想的仿生吸能结构。
1.1.2 泡沫结构
泡沫结构是一种典型的多孔轻质结构。当外力作用于泡沫结构时,泡沫支撑部分的形变和内部空间压缩能够有效地分散外荷载,从而减少冲击、压缩等外力传递给其他部分的可能性。因而,泡沫结构是一种理想的吸能材料,能够提供吸能功能而不会显著增加其质量。国内外已经把高性能泡沫结构作为承载的结构在航空航天、交通运输等领域使用。
图3
丝瓜海绵具有大孔和微孔的分层细胞结构,而大孔周围坚硬的内表面层大大提高了其强度,An和Fan[36]为模拟这种层次化的生物细胞结构将薄壁碳纤维增强聚合物管嵌入到铝泡沫中,构建了一种类似葫芦海绵的分层泡沫结构(图3(a))。此结构中的碳纤维增强聚合物管可采用增材制造制备。在单轴压缩实验中,与未嵌入碳纤维管的泡沫圆柱体相比,其SEA能量吸收能力与单独由铝制成的泡沫圆柱体相比从40.0%提高了至73.0%,具体的提高幅度取决于泡沫的密度。此外,莲藕也为学者们的泡沫结构设计提供了新的素材。莲藕具有彼此平行的长圆柱形孔状微观结构,Tane等[37]参考此独特的多孔结构,采用连续区域熔融的增材制造技术制备了一种圆柱形空腔多孔结构(图3(b))。空腔内部的圆柱形微结构沿固化方向排列,在动态压缩下,发现该结构具有宽范围的平台应力区域(高达300 MPa,宽达45%),因此其可吸收的能量比具有各向同性孔泡沫结构高6倍。以上两种自然结构相对较软,在自然界中还有一些相对较硬的泡沫结构。箱龟外壳是一种由层状骨壳和内部闭孔泡沫骨网络组成的三明治复合结构,其中骨层密度很大,泡沫层则具有较大的孔隙密度偏小,这样的结构特点使其具有超强抗冲击能力的同时,也保持着内部的生物行为。受其启发Rhee等[38]设计了几种能够使用增材制造制备、与箱龟壳层结构类似的泡沫铝结构(图3(c)),并发现仿生泡沫结构与其他天然大孔泡沫结构的SEA相比,增加了10%至30%。柚皮处于柔性泡沫形态时,由实心和空心两部分组成,实心部分用来分散热量降低表面温度,空心部分用来蓄水为柚皮提供新鲜水分,这样的结构特性使其具有较高吸能性的同时还保持着质量轻的优点。于是Zhang等[39]以柚子皮对果肉屏蔽保护为灵感,利用金属3D打印技术,设计了一种类柚子皮的仿生多孔结构(图3(d)),该结构不但具有散热功能,还具有高的吸能能力(SEA为13.2 J/g),这优于大多数晶格或多孔金属泡沫超材料,即在吸能上得到了优化。
1.1.3 夹心结构
夹心结构一般由柔软的内层夹和两个坚硬的外壳构成,该结构可以在遭受意外碰撞时通过塑性变形来吸收冲击能量,因此具有良好的冲击能量吸收能力。
图4
在自然界中螳螂虾的趾突可以承受高达1500 N的冲击力而不发生灾难性断裂,其趾突由一个厚的块状成分和一个薄的撞击层组成,厚的块状成分由一个极其有序的人字形图案组成,呈正弦排列形式,这种排列增加了裂纹扩展路径长度,显著提高了能量耗散能力,具有强大的吸能特性。参考此结构,Yang等[40]设计出一种新型的轻质仿生双正弦波纹(Double-sine corrugated,DCS)夹层结构(图4(a)),该结构模仿螳螂虾外壳利用两个不同的波纹方向来增强结构吸收能量的能力。并对该结构进行准静态均匀压缩实验,结果显示与常规正弦波纹芯夹层结构相比,仿生双正弦波纹(DCS)夹层结构的比吸收能量SEA是其1.7倍。这为利用增材制造制备能量吸收结构提供了新的设计思路和方法。
Lee等[41]通过透射电镜观察啄木鸟上喙发现其上喙是呈多孔状、密集角蛋白颗粒的蜂窝状结构(图4(b))。然而,与传统的蜂窝状结构不同的是,啄木鸟喙的蜂窝状结构的细胞壁呈波浪形正弦结构状,这种波浪状结构可以提高鸟喙的硬度、吸能性能和损伤容忍度。基于此,Ha等[42]设计了一种新型仿生多孔蜂窝夹层板(图4(c)),板壁被设计成波浪状,并对这种新型夹层板进行纳米压痕测试,结果表明在芯材厚度相同的情况下,新型夹层板的比能量吸收量是标准蜂窝夹层板的1.25倍。
在自然界中叶片的叶脉可以使水分和营养物质通过叶片,还有助于保持其形态,防止裂缝的扩散,叶片中叶脉这种强韧的属性,为加强夹心层结构提供灵感。
Sun等[43]受此启发设计了一种加强夹层结构的软蜂窝芯(图4(d)),即在蜂窝芯中嵌入了周期性的仿生网格,这种网格即充当着树叶的强韧脉。随后对其进行面内压缩实验,结果表明,加强夹层结构的刚度和比能吸收比相较于传统蜂窝三明治板分别高出5.3%和125%。这种加强夹层结构为使用增材制造开发更高性能的轻质夹层结构提供了一种新颖的设计思路。
目前在仿生吸能结构领域中,通过模仿生物结构可以设计出更轻便和高强度的材料,这些仿生结构可以吸收更多的能量,具有超高的抗冲击性能。但是由于仿生结构的拓扑复杂性,需要使用3D打印等先进技术进行生产,这会增加其生产成本。对于一些使用3D打印生产的仿生结构,还会由于打印技术的局限影响仿生结构的力学性能,使其与理想值有一定偏差。
1.2 高强度
自然界中的高强度结构通常具有多层级、梯度性、特殊几何形状等特点。得益于这些结构形态的启发,人们发展了多种高强度仿生结构。伴随着与纤维增强复合材料等轻量化材料的结合,这些拥有高强度、高耐用性的仿生结构在航空航天等工程领域中有广泛的应用前景。
1.2.1 高强度蜂窝结构
蜂窝结构在自然界中十分常见,其材料主要分布在外壳和支撑区域,此结构特征使应力能够均匀分布到整个结构中,而不会集中在特定区域,均匀的应力分布有助于减少应力集中和损伤的可能性,提高结构的强度和韧性。此外蜂窝结构的胞元之间可以沿多个方向相互支撑。这种多向支撑能够分散外部应力的作用,减少结构的变形和破坏风险。这种独特的机制使蜂窝结构具有强大的承载能力,并让蜂窝结构成为热门的仿生结构之一。
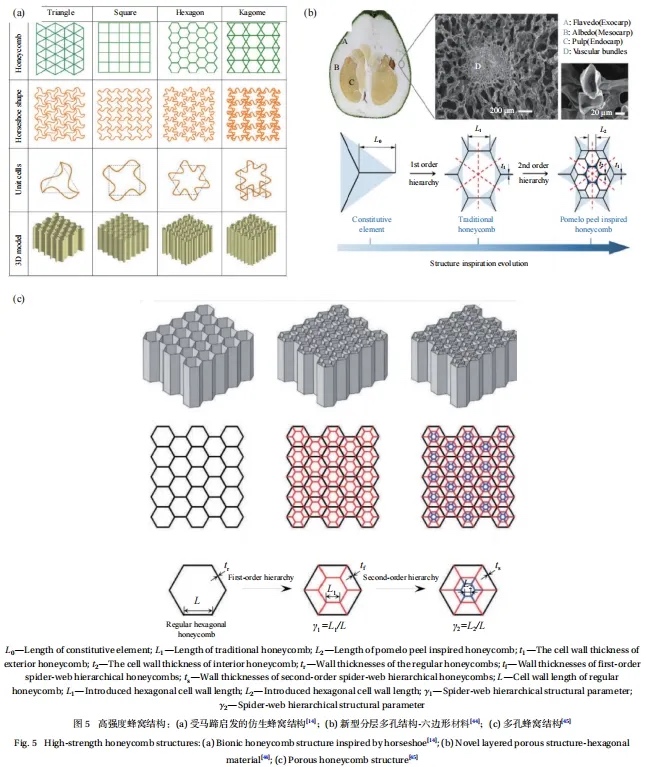
图5
(责任编辑:admin) |