依靠天然气工作的熔炉中,在 1200°C 温度条件下且过量空气为 10% 时,如果不使用热回收设备,则 63% 的输入能力将会随废气损失掉,而无法回收到过程当中。3D打印技术开辟了新的可能性:增材制造的系列部件将为热加工技术的能源转型做出重大贡献。在这方面,借助 3D 打印,可以生产出表面积更大的复杂结构,从而提高整个系统的效率。全新开发的 IntrinSiC© 换热式燃烧器或 IRecu,用于间接加热热处理炉。该产品利用了 3D 打印的所有灵活性。凭借 3D 打印的陀螺结构,它将能源效率最大化到前所未有的水平。
© Kueppers Solutions GmbH
逐步实现碳中和
根据3D科学谷,新设计与3D打印工艺的结合,将诞生全新的市场机遇,创造飞跃的制造附加值,带来更可持续的人类社会发展前景,3D打印-增材制造正在向多维度的深化层面发展。
新型蓄热式燃烧器 iRecu
根据3D科学谷的市场了解,Kueppers 开发的新型蓄热式燃烧器 iRecu ® 使用数学上复杂的结构作为热交换器:三重周期最小曲面(简称 TPMS),TPMS结构是一种的典型的为增材制造而设计的结构,它们既具有高强度重量比,又具有非常高的表面积质量比,多被集成在需要进行热交换的3D打印部件中,例如热交换器、散热器。
这种复杂的设计没有3D打印就无法制造出来,通过这种结构,在当今的标准尺寸中可以实现 90% 的更高效率。自恢复式燃烧器 iRecu ® 的整个流程链——从CAD 模型的创建到成品的制造——是 100% 数字化的,意味着最大的灵活性。此外,还减少了成本和时间,3D打印带来的数字流程链和制造过程的自由度使得在批量生产中提供为客户流程单独设计的“定制产品”成为可能。 三重周期最小曲面 (TPMS) 是平滑的无限曲率曲面,平均曲率为零,将 3D 空间划分为两个共连续相。TPMS 结构由于其光滑的表面和均匀的曲率而增强了增材制造能力,可以实现自支撑制造。
在这个案例中,热加工系统实现碳中和的三个步骤:
第 1 步:使用 TPMS 优化设计的热交换器使得化石燃料更有效,减少二氧化碳排放
使用化石燃料时更有效的热回收减少了所需的能量,因此也减少了二氧化碳排放。可以显着降低运营成本。在 1,000 °C 的过程中,目前使用天然气运行,无需预热空气,用新型蓄热式燃烧器 iRecu ®的系统替代意味着节能 40%。陶瓷和金属换热器已经被用作热交换器。然而,到目前为止,这些都是带有肋条或旋钮以增加表面积的简单管子。这些几何形状的优化潜力非常低,需要创新的解决方案来提高热回收效率并加速能源转型。
3D 打印的 TPMS 结构
为了更好地说明,新鲜空气通路用灰色表示,废气通路用红色表示。
© Kueppers Solutions GmbH
在换热式燃烧器领域,除了效率之外,氮氧化物的排放也是一个关键因素。由于燃烧空气的预热,整个燃烧反应在明显更高的温度水平下进行。促进了热氮氧化物的形成。这就是 Kueppers 采用新开发的增材制造的燃气-空气混合装置的优势,尽管燃烧空气温度很高,但它仍远低于法律限制。
第 2 步:化石燃料和可再生燃料的混合运行
全世界范围的国家氢能战略重点都在关注氢作为可再生燃料气体,当前的燃烧器系统必须进行调整或更换以允许结合使用两种燃料气体。双燃料混合装置可以以稳定、安全的方式燃烧天然气、氢气或两种气体的任何混合物,并符合法定排放限制,即使两种燃料气体具有非常不同的燃烧特性。
自恢复式燃烧器 iRecu ® 这种双通道混合单元只能在金属3D 打印中实现,具有相应的制造公差(±0.1 毫米)和自由度。
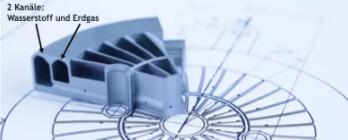
双燃料混合单元,两个独立的通道系统集成在一个组件中,用于燃料天然气和氢气。
© Kueppers Solutions GmbH
预计2022年将提供首批绿色氢源,然而,在未来几年内,这一数量将不足以立即转换为 100% 氢气。因此,通过混合运行的双燃料混合装置,可以交替两种燃料的使用。
第 3 步:转换为 100% 可再生燃料
在不久的将来,从 2030 年左右开始,将有足够的绿色氢气从混合运行转向 100% 无二氧化碳生产。然后可以在不修改系统的情况下进行这种转换。只有天然气的燃料通道将在工厂停止使用并关闭。iRecu ® 可以节省化石燃料和可再生燃料,并有效地产生过程热量。尽管再生燃料稀缺,这已经可以向能源转型迈出重要一步。仅在德国,热加工行业的二氧化碳排放量就与汽车行业的排放量相当。几乎所有需要 600 °C 至 1500 °C 高温的工艺也会产生相应的高温废气。很大一部分热能通常在过程中损失,在3D科学谷看来,在所有创造价值的源头,在所有可能颠覆的源头,算法无疑是最重要的部分之一。实现高强度重量比,又具有非常高的表面积质量比的TPMS也是算法的一种,与增材制造技术结合起来,使得设计师能够创建兼具高强度和散热特性的多功能结构。
通过软件应用TPMS
nTopology 公司的设计师通过nTop Platform设计的散热器实现表面积最大化,同时实现质量最小化。设计师使用了三重周期性最小表面(TPMS),对于结构应用而言,该设计显示出高强度重量比。该设计如果与增材制造技术结合使用,将使设计师能够创建兼具高强度和散热特性的多功能结构。
具有不同周期性和厚度的三种TPMS结构。
© nTopology
nTopology 对Gyroids(螺旋),Schwarz基元和Lidinoids 这三类TPMS结构进行了研究与评估,其中每种类型的结构都是正弦和余弦的线性组合,而这些组合会在三维空间中形成周期性的波形几何形状。根据3D科学谷的了解,就像二维波形一样,设计的可能性可以通过改变这些方程式的幅度和周期来实现,通过将这些设计输入与实验设计(DOE)方法结合起来,可以准确地评估这些组件的性能。
随着热量的散失,对流自然会导致空气流过散热器的散热片。TPMS类型散热器的旋转鳍片可增强边界层混合,与传统散热器设计相比,具有提供更高有效表面积的潜力。
nTopology 进行了简单的数值研究,从而找出性能最高的TPMS散热器,即设计输入可最大程度地增加表面积,并最大程度地减少最终散热器的质量。设计师使用nTop Platform 计算几何内核以及分析方法进行了实验,设计师可以快速进行几何更改并评估设计输入的性能输出。从上图中可以看出哪个设计的表面积最大。
(责任编辑:admin) |