3D打印一体化结构是一种具有代表性的为增材制造而设计(Design for additive manufacturing,DfAM)的结构。以增材制造的思维去设计时,需要突破以往通过铸造、压铸、机械加工制造所带来的思维限制,这个过程是充满挑战的。近日,特斯拉公开了其具有典型的创成式特点的结构一体化车后架图片,这为设计者和制造者带来了一次脑洞大开的体验。
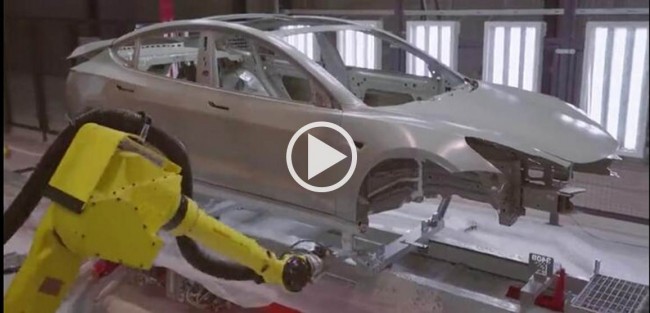
视频:特斯拉上海超级工厂全方位直击
产品性能飞跃,驱动制造技术由点至面发展
在特斯拉的后车架设计上我们可以清晰的看到创成式设计的特点。从创成式设计中所获得的好处远不止轻量化,创成式设计与3D打印技术的结合将原来的许多零部件合并为一体实现结构一体化,并且能够显着压缩产品开发过程。工程师可以获得数百个可供制造的设计选项,这些选项是他们无法手动设计的,而且只需要花费一小部分时间来验证单一设计,结构一体化带来供应链的压缩和组装成本的降低。
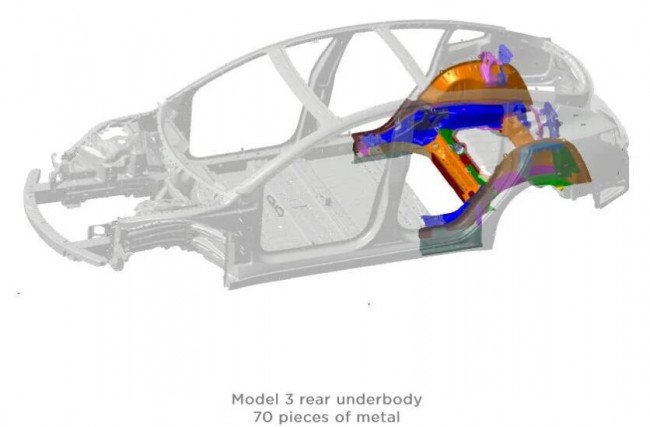
特斯拉3后车架由70个零件组成
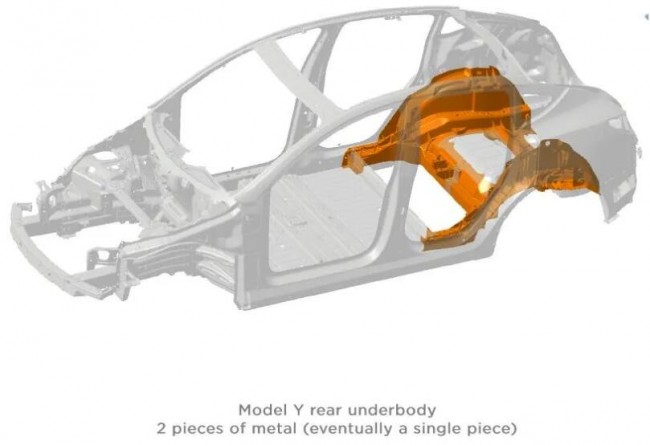
特斯拉Y后车架由2个零件组成(最终将简化为1个零件)
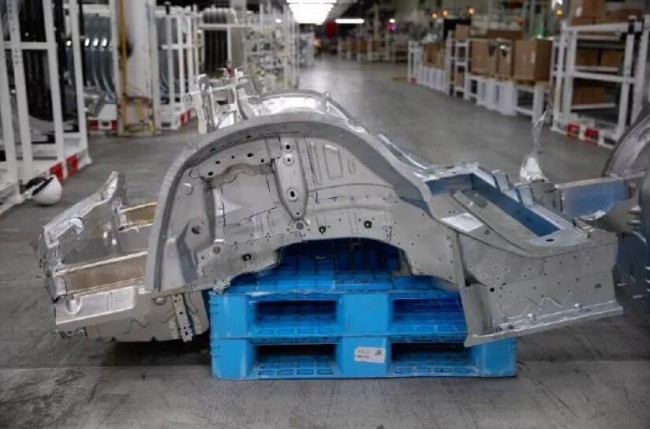
特斯拉3后车架由70个零件组成-实物图
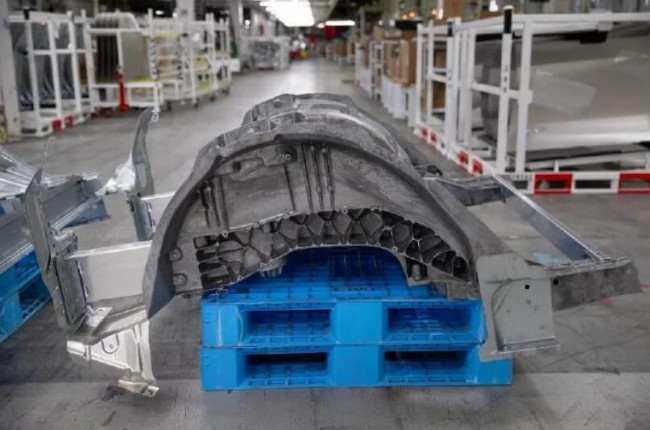
特斯拉Y后车架由2个零件组成(最终将简化为1个零件)-实物图
而对汽车一体化结构的探索,国际上Altair、APWORKS、csi, EOS、GERG与贺利氏(Heraeus)曾利用金属3D打印技术对大众开迪汽车前端构造进行再制造。前端构造包含了主动冷却和被动冷却的细节设计,例如用于冷却电池和刹车系统的气流管道。另外,热处理、被动安全和液体贮存相关功能,也被整合进前端模块的仿生学负重设计中。附加功能与结构相结合的一个例子就是浸液罐,它可以整合进前端构造。遵循着这些目的,设计师开始设计、开发并建造前端结构。
3D打印的一体化结构实现,即用最少的部件配置满足最多的技术性能需求,将为汽车制造提供创新性的思路。
面对这些一体化结构件的脑洞大开,我们应该如何?是置若罔闻还是该有所思索?
正如《暗知识》一书提到的”预测未来永远有风险,但可以促使自己深入思考,也能引起有质量的讨论。为此,我们必须留意那些“蠢蠢欲动”的点,培养对趋势的直觉与敏锐度,提前布局与准备,才不会在未来已来的明天陷入被动。根据3D科学谷的市场观察,目前3D打印技术在新能源汽车制造领域的切入点正是制造轻量化部件与热管理部件。
关于3D打印与产业化应用的结合,3D科学谷曾经做过一个深度的思考与讨论:如今的3D打印技术发展程度,在技术层面上速度远超我们的想像,具备了在很多应用层面颠覆的潜能,而在经济性的层面上发展的到底如何呢?拿汽车产业来说,3D打印目前无疑在100万-200万价位的车型上展开了产业化的应用,那么这样的发展趋势将在什么样的时间节点发展到50万价位的车型?当发展到20万-30万价位的车型的时候,占据主流的3D打印技术又将是哪一种类别的技术?
Model Y是特斯拉推出的第五款车型,也是首款中型纯电动SUV,新车于2019年3月正式发布,其外观设计延续了Model
3的设计语言。在特斯拉中国官网上,Model
Y目前显示最快将于2021年开始生产,其中长续航全轮驱动版的预售价为48.8万元,Performance高性能版的预售价为53.5万元。
特斯拉对自己使用的3D打印技术严格保密,如果Model Y的后车底的结构一体化通过3D打印技术结合传统技术实现,那么这意味着3D打印技术的产业化应用从100万-200万价位区间的车型移动到了50万价位的车型,这对3D打印技术的发展来说是令人激动的。
虽然我们并不知道特斯拉将使用什么样的技术,然而结构一体化与轻量化的结合是新能源汽车抢占技术发展前沿的一大努力方向。根据3D科学谷的市场观察,弗劳恩霍夫激光技术研究所(Fraunhofer ILT)名为MultiPROmobil 的研究项目就涉及到了开发一种可实现切割、焊接和增材制造(3D打印)三种功能的激光加工头,这项创新技术钣金加工行业将为提供显著的生产力和质量优势。
MultiPROmobil 项目中的四个合作伙伴通过开发这款多功能激光加工头,应对新能源、电动汽车制造领域不断变化的生产和技术挑战。根据Fraunhofer ILT,新能源汽车设计迭代快,产量大小存在波动,新能源汽车制造商对于创新的生产理念的追求,使得新能源汽车的生产需要在灵活性和生产率之间取得平衡。
MultiPROmobil合作伙伴使用高度灵活的工艺链,可以数字化显示新的车辆组件,然后对它们进行测试和评估。在项目合作伙伴LBBZ所打造的工业环境中,带有多功能激光加工头的机器人,将能够制造新能源汽车的仿生车辆结构。该技术的第一个应用示例为电动车辆的三角形控制臂,该部件将在优化设计和切割后,在多功能激光机器人单元中进行焊接和增材制造。而完成这些制造流程,不需要更换激光头。
根据MultiPROmobil 项目参与者的预测,该技术可使新能源汽车制造商工程效率得到提高,启动时间减少约30%,单位成本和资源消耗有望至少降低20%。
当然,类似于Fraunhofer
ILT的MultiPROmobil这样的技术是实现轻量化汽车结构件制造的基础。在工作中,设计工程师会遇到很多挑战,存在的痛点包括如何获得最优的结构形状,如何将最优的结构形状与最优的产品性能相结合起来设计等。设计是另外一个重要的解锁结构一体化应用机会的因素。
突破传统设计思维的限制是一个需要用户与3D打印企业长期共同努力的过程。除此之外,增材制造软件的应用也是推动增材制造思维的力量。近年来,Ansys、Autodesk
、Altair solidThinking
等软件公司为设计师提供了智能化的为增材制造而设计的工具。欧特克netfabb等软件,为培养增材制造(DfAM)理念提供了相关的深化软件,这些软件具有支持文件编辑、切片、以及点阵结构设计和拓扑优化零件的变形模拟等功能,将设计与3D打印有效的结合起来。而对于复杂的工程来说,还需要更大的端到终端的软件解决方案的支持。例如,西门子的PLM增材制造产品生命周期管理系统和达索的3DExperience平台,这些软件都将DfAM的理念进一步演绎到更系统化的范畴内。
随着结构一体化在新能源领域应用的切入,能在未来5年内跑赢市场的应用点,将实现由“点”及“面”,从一个角落瞬间“掀起”,“跳跃”起来,塑造变化的大局,而3D打印在实现结构一体化方面有着天然的成本优势,必将随着能在未来5年内跑赢市场的应用点,将实现由“点”及“面”的应用发展获得一条新的上升路线。
正如同时掌管着SpaceX与特斯拉的首席执行官马斯克所提到的:通过3D打印,可以以传统制造方法的一小部分成本和时间就能制造出坚固且高性能的发动机零件。我们相信,通过3D打印可以在汽车制造方面实现更为轻量化的结构一体化零件,从而提升新能源汽车的整体性能。为此,我们需要从制造技术和设计等多方面做好准备,以迎接从点到面的发展机会。
(责任编辑:admin) |